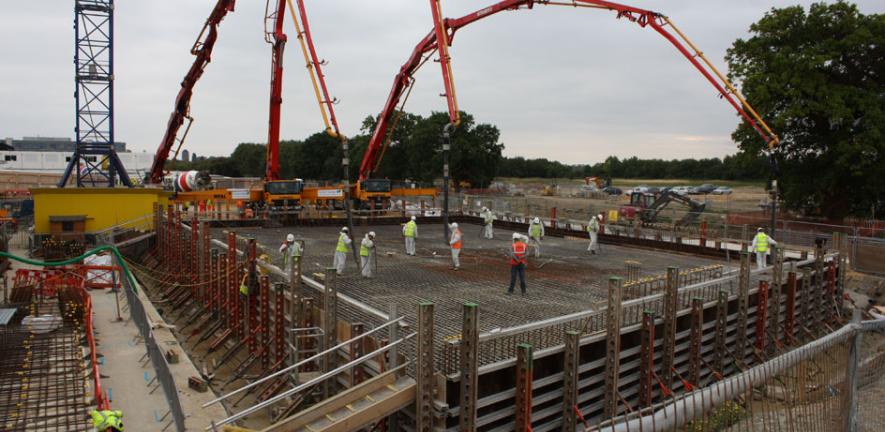
A major construction logistics operation was staged on the West Cambridge site recently to create a substantial concrete base for some of the world’s most powerful microscopes.
A major construction logistics operation was staged on the West Cambridge site recently to create a substantial concrete base for some of the world’s most powerful microscopes.
Construction is well under way on the new £41 million building for the Department of Materials Science and Metallurgy.
The Department of Materials Science and Metallurgy is committed to making significant advances in the synthesis, processing and patterning of materials to deliver enhanced performance, and addressing issues of sustainability and the scarcity of resources.
Observing the smallest particles that make up matter requires a highly stable environment and this presents a key challenge in the design of the new facility.
The University’s Estate Management, led by director Michael Bienias, assembled a team to design the new building in 2009. Since then the architect, NBBJ, structural engineers, Ramboll, and services engineers, Hoare Lea, have been hard at work to define the requirements and to design a building to give the department the world class facilities needed for its research.
One part of the building will house the Electron Microscopy (EM) suite which has seven highly specialised microscope rooms. The requirements for these rooms are highly complex and exacting. For the microscopes to function correctly external influences must be minimal; electro-magnetic interference, temperature fluctuations and the most minute vibrations can all effect the clarity of the images achieved.
Each of these requirements has led to special design considerations in all aspects of the building. To give both excellent anti vibration and thermal properties the building uses heavy weight concrete construction sitting on a 2m deep solid concrete foundation slab which is sunk into the clay soil on site.
This massive base gives the mass and stability to improve the ambient vibration properties on site and means that the microscopes will be unaffected by traffic movements on the nearby roads and motorways which could otherwise affect the imaging work.
The concrete base for the EM suite contains 1350m3 of concrete which had to be poured in a single day. Doing this eliminates joints in the foundation which could lead to weaknesses in the slab. Pouring this volume of concrete in one go was a special undertaking which the project team had been planning for the last year.
Lynden Spencer-Allen of Structural Engineer Ramboll explains “A normal size concrete pour would be about 1/5th of the size of this pour and still take all day. This pour was therefore quite unusual and required the design, logistics and planning to be spot-on”.
The logistics of delivering approximately 200 concrete lorry loads of concrete in a single day required planning in minute detail.
Four concrete batching plants were in operation all day solely on this project.
The notorious Cambridge traffic led to the project team opting to carry out the pour on a Sunday.
Estate Management Project Manager, Brian Lees explained: “During construction works we always try to minimise disruption to our neighbours, but the benefits of carrying out this work on a Sunday were obvious.
“By reducing the logistical risk we allow the pour to be closely controlled rather than risk overrunning and causing night time disruption instead. We worked closely with the contractor Willmott Dixon to ensure that everything was done to make the day pass smoothly for all interested parties. We liaised closely with the City Council to obtain the special dispensation required to carry out the work at the weekend.”
With so much concrete poured the environmental sustainability of the scheme is an obvious question.
“Sustainability has many aspects. Giving the department a world-class facility is an enabler for future scientific discovery that could change the way we live,” says Lynden Spencer-Allen.
“On a practical level we have been careful to reduce the environmental impact of the concrete. Cement production is the most energy consuming aspect of concrete but we reduced the impact by replacing 70% of the cement with material that is a waste by-product from steel making. This gives a significant reduction in the embodied carbon of the concrete. It’s also beneficial for the properties of the concrete so it’s a win-win situation.”
This may only be the start of a long construction process, but with each step the department is closer to moving into a new world class facility at West Cambridge.
This work is licensed under a Creative Commons Licence. If you use this content on your site please link back to this page.